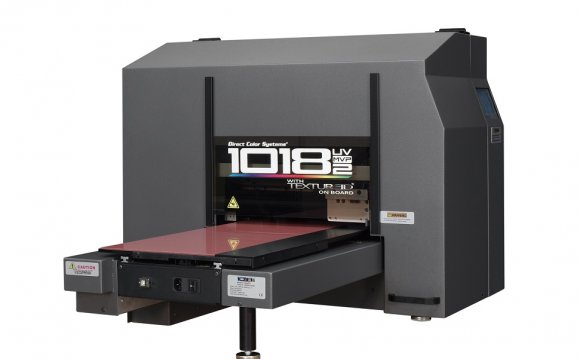
When you compare the differences between conventional printing techniques – such as for example pad and display screen publishing – and electronic inkjet publishing, we prefer to utilize the analogy of evaluating a 1969 Camaro to a 2014 Tesla. They’re both cars, and so they can both allow you to get where you are going, however the ways of how they work while the price of procedure can be various. Old-fashioned printing always has been finished with direct contact of the inks via an automobile particularly a pad, display screen or blanket into item becoming imprinted. Inkjet deposition is done through a non-contact kind of publishing with specified offsets of the heads towards substrate being imprinted, thus eliminating pads, displays, dishes, kind put and stamps.
Traditional forms of printing will have been a technical procedure, and inkjet is a computerized process. The biggest solitary advantage of the electronic process may be the capacity to vary from one visual to the next aided by the click of a mouse. Not any longer can there be the requirement to alter screens, pads, plates and registers amongst the colors for each individual print process. For companies printing quick runs or dynamic data, the occasions savings are dramatic. However, there are also advantages to conventional kinds of publishing.
Question: so how exactly does ink adhesion vary?
Solution: standard forms of publishing have been in existence for decades, generally there is an enormous historic understanding base. Inks were tested on different substrates, so we know what pre-treatments, variety of inks, ingredients and post-curing processes have to be applied for different print scenarios. In comparison, UV-curable inkjet publishing is quickly building, but with little historical knowledge.
The primary concerns when utilizing pad or screen publishing inks have been adhesion and drying out time. Specific materials, such as for instance olefins, usually need a pre-treatment to obtain the correct area tension for adhesion. Occasionally, static and area contamination can justify some changes into the inks.
Unlike old-fashioned pad/screen printing inks, adhesion isn't the only nervous about the UV-cure digital inks; wettability (dyne amount) plays a big part in obtaining an excellent print. The wet out of the printing is really what provides a definite, smooth, high quality image. In the event that imprinted dots encounter surface stress, static or contamination, the dots will bead up-and create a grainy image. Heat can be used to regulate inkjet ink viscosity versus analog inks in which additives (thinners) are used. Environmental results on all ink methods tend to be a factor to consider, and moisture control and heat perform a vital role in print quality in both inkjet along with other older technologies.
Matter: exist color limitations with digital inkjet?
Response: when working with electronic CMYK Lc Lm inks, it is critical to understand that you can find restrictions to color-matching. Big brands have especially created colors that represent their products. These are easily coordinated in standard forms of printing by combining inks to produce a desired color. But making use of custom colorants on electronic devices is quite unusual because of their price, the development some time the difficulty (if you don't impossibility) of altering colors and cleansing ink feed systems after usage without contaminating the next shade. It’s already been calculated that just 30 to 40 % of Pantone colors is possible making use of a regular digital CMYK. That departs a significant portion of brand name colors not in the doable gamut, whether they’re specified using Pantone or perhaps not. Most brand name owners know about these limits and recognize that a perfect match for many large chroma colors is unachievable and accept that close is close enough.