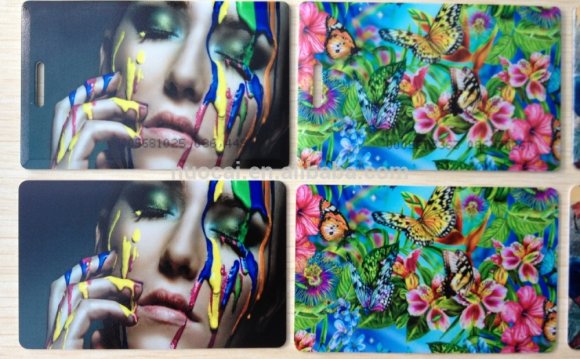
Those who know myself, or who've attended the Inkjet Academy training course that I jointly present with Dr Alan Hudd, know that I’ve been outstanding advocate of taking ink offer and nozzle upkeep really through the concept phase of establishing a new item. These are generally undoubtedly crucial components of desk-top items, and their cautious design and optimisation can result in trustworthy manufacturing presses also.
The usage of inkjet for high-speed printing applications – commercial and packaging printing in specific – features required the introduction of page-wide fixed range printheads. Printing at high-speed with thousands of nozzles causes some other problems too, and I’m likely to explore three of them in this weblog.
Will you be wondering the way I know about these problems? They don’t get mentioned in public places in most cases. Do we hang around in pubs near to manufacturers R&D labs looking to overhear discussions after a tough day’s development? No, nothing that exciting. I study patent applications.
Ink misting
Printhead producers and ink formulators try to optimise the jetting process between them, often perhaps not a simple cooperation as they typically work with different organizations. But regardless of how elegant the fall development procedure might appear, utilizing an optical fall monitoring system, you will have microscopic fall fragments developed during the point where end for the fall breaks out of the nozzle. These tiny, often sub-micron-sized fragments of ink, don't have a lot of forward momentum and tend to move because of the environment currents across the printhead. In high-speed printing the substrate passes underneath the printheads, drawing environment along side it. The turbulence this produces distributes the ink mist for the other countries in the device.
Condensation
Aqueous inks would be the option for most brand new presses under development. However these require substantial dryers within the hit. At extremely high rates it may be necessary to warm the internet before, or right after, publishing. Operating from the water-carrier can increase the print high quality by stopping excessive bleed and consumption in to the substrate. But it also results in the creation of large amounts of liquid vapour. Just like kitchen area windows if you're cooking, this water vapour will condense on anywhere cold sufficient; like the printheads and mountings inside the hit. And also as it builds it's going to trickle on the substrate and destroy the beautiful print you have worked so very hard to create.
Drop recognition and missing/misaligned nozzle correction
When you've got tens and thousands of nozzles, there is the issue the failure of one of all of them could conceivably impact the high printing quality demanded by these applications. You can find great technologies for concealing any artifact due to a missing or misaligned nozzle – for example by increasing the dot size each region of the lacking nozzle, or substituting a different colour. But you can only play these tricks if you know which nozzles are evoking the dilemmas. Technology is therefore being created to either look at the falls in-flight, or even the imprinted image, to take into consideration these problems. Taking into account the number of nozzles involved and print speed this is not a trivial concern to conquer.
When the truth is the impressive brand-new inkjet presses at Drupa 2016 think of the issues the engineers have had to tackle. Several of dilemmas are not extremely glamorous, but they all need satisfactory solutions to provide dependable systems.